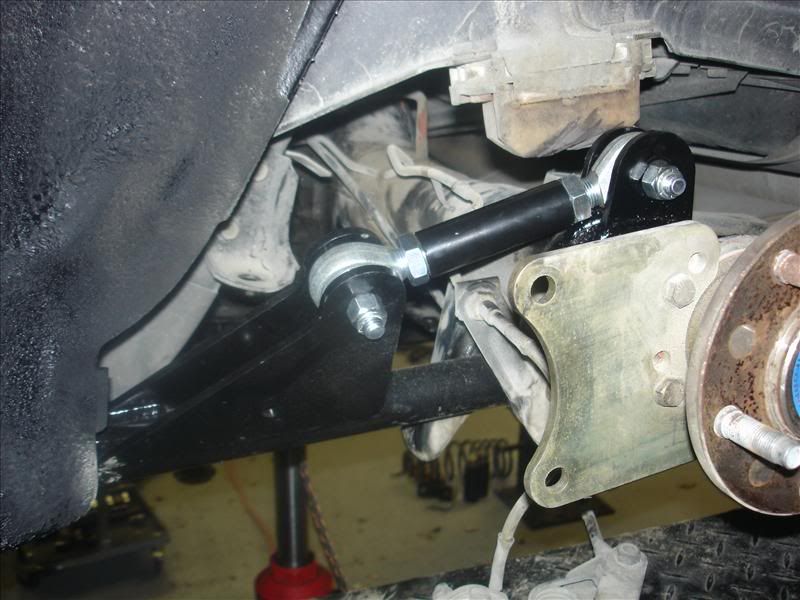
I can see something like that working for a driver or a car with low horsepower. It is essentially in charastics like using a short, very short ladder bar and mounting the front pivot high.
I have a set of ladder bars that are using that same short link at the top but they are not that short and are very well braced. One of thse days I will see if anyone wnts to buy them.
Tying the top to the bottom is nothing new at all. Problems I see with that is it ends up being a single round bar on each side to handle all the torque and suspension action. Can work with low power.
The same basic idea from a structural and suspension viewpoint was done back in 1964 by Ford Motor Company on the Comet Super Cyclones and the Ford Thunderbolts. EXCEPT Thiers was stronger. They tied the rear end housing to a single bottom bar with welded gussets and used a single front pivot on each side, but their single bar was a piece of 2 x 3 inch square tubing. That little round bar of theirs in the pic just won't do the job if you have power and traction.
No way under the sun you can make that think work with high power with tires hooking.
I don't see anything wrong with his out board shock mounting but I quetion why. If it is to be able to mount a coilover with a long travel i understand. Doesn't leave much room for tires though.
I think it would be as economical to just do a full changeover to either a 4 link or ladder bar setup for what that kit is selling for though.
System Includes:
Two lower control arms made from 1.50” diameter thick walled tubing (1/4" wall) with oversized bushings pressed into the ends, two double adjustable upper control arms made from 1.25” diameter thick walled tubing (1/4" wall), four upper control arm mounting brackets made from 1/4” thick laser cut steel, all necessary hardware, and detailed instructions.
* System requires welding of the new upper control arm mounting brackets to the axle.
* System may require minor trimming of the wheel well for clearance for the upper control arm mounting brackets.
No doubt that short high instant center will hook.
My thoughts are that the company or person that has come out with this has over engineered himself.
Ed